The cattle feed manufacturing plant has stood out since it makes the recycling of waste plastics simple. Poultry feed machine normally describes plant granulator and also corn and also soybean meal granulator. The die head is a fundamental part of the poultry feed making machine. Today, let me discuss just how to cleanse it.
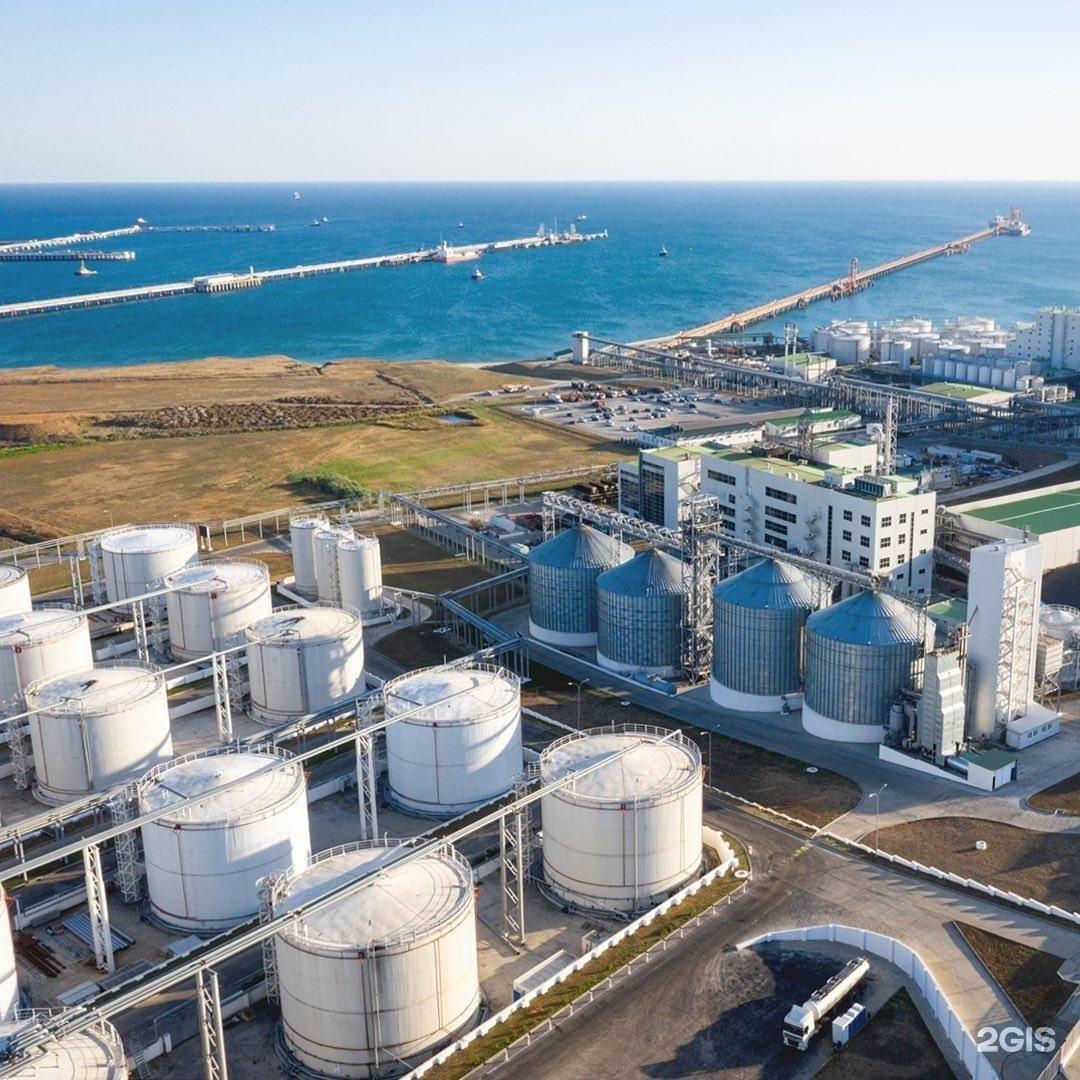
( 2) Hand-operated methods can be used. Usually, we replace the internet by hand, open the net by hand, and shovel the plastic mold with a tiny shovel. The manifold is straight heated as well as burns with the cleanest gas.
( 3) Gas welding is labor-saving to shed, yet it is not eco-friendly and also is bad for equipment.
( 4) Find soluble solvents with high cost and inadequate feasibility.
It is really essential to clean and also maintain the ring die feed pellet machine for poultry. The ring die poultry pellet machine need to be on a regular basis preserved throughout use, and also timely cleansing can prolong its service life.
1. Factors and also services for the poultry feed granulator not feeding
( 1) The wetness material of the product is not appropriate. Excessive or insufficient dampness in the product will block the die hole and also cause the pellet making machine for poultry feed to not release. In this case, inspect the summed product to maintain the wetness between 10% -15%.
( 2) The die platen and also stress roller are seriously used. The die platen and also the pressure roller are the major accessories of the cattle feed manufacturing plant, and they are also prone accessories. If the accessories are aging or malfunctioning, it is additionally the reason that the poultry food handling machine does not product. If it's a new cattle feed manufacturing plant, you can inform which is the problem by simply looking at which accessories aren't working. If the poultry food handling machine has been made use of for years, the accessories are maturing as well as can be changed.
( 3) The compression proportion of the mold is not appropriate. Different materials need various compression proportion molds. Picking a normal large maker will certainly be tailored according to the client's needs. Normally, this issue does not occur. If there is no material, examine the compression ratio of the mold and mildew. Otherwise ideal, change the product mold and mildew.
( 4) The product has high crude fiber material. Poultry feed manufacturer machines are available in various versions and also powers. For various versions of cattle feed manufacturing plants, the granulation demands are additionally various. Some poultry feed manufacturer machines appropriate for pressing coarse fibers and some are suitable for pressing fine fibers. If you choose a small poultry feed making machine to push crude fiber materials, it is also the reason the poultry pellet granulator does not create product. Option Interact with the manufacturer to change the poultry feed pelletizer.
( 5) The range in between the mold and mildew as well as the roller is not ideal. cattle feed manufacturing plants promote pellet development by squeezing accessory rolls and also dies. If the spacing is not appropriate, it will certainly also cause the pellet machine to fall short to feed normally. The solution is to change the spacing.
( 6) There is collected material in the poultry feed maker machine. After the cattle feed manufacturing plant is produced, there will be some accumulation, and also no tidy deposit will be released. After the next procedure of the poultry pellet making machine, because of the high temperature, it will strengthen into a hard block, causing the poultry making machine to fall short to release typically. The remedy is to clean the inside, clean up the debris.
3. The brand-new method of cattle feed manufacturing plant, a lot of farmers use it incorrect!
A lot of farmers know that there are just a couple of ways to utilize the pellet mill. For example, for poultry, the farmers feel that it is extremely simple, does not need expert abilities, as well as basically recognizes it if they do not know how to look. However, what appears to be simple is in fact not straightforward. The entire process of the cattle feed manufacturing plant from feeding to discharging calls for several precautions:
( 1) Bit size of material crushing
Most of us know that, according to the different feeding attributes of animals, the bit size of the cattle feed manufacturing plant is also different throughout the pelleting procedure. But there are still misunderstandings regarding what to smash as well as what to granulate.
In general, the fragment size of the crushed material is related to the pressed diameter in the cattle feed manufacturing plant. When the conventional products are crushed, the diameter of the general pushing has to do with 6 mm, and the fragments listed below 6 mm belong to unique poultry residential properties, while the general conventional feed is pressed in the variety of 6 mm.
( 2) Feed pelleting moisture
Many farmers do rule out the trouble of water when utilizing the poultry feed processing machine, which will bring about the granulated product being soft as well as unshaped, leading to bad pet feed consumption. Nonetheless, the actual pelleted feed items are pelleted by the concept of dry in and also dry, so the water requirements in the pelleting procedure are really strict. The dampness content of the powder is managed at regarding 13%, to ensure that the compressed particles are usually fuller and also the finished product impact is great.
( 3) The machine feeds at a consistent speed
Whether the cattle feed manufacturing plant is fed at an uniform speed is a trouble that most farmers neglect in the process of use. The length of the uniform speed directly affects the normal operation of the poultry pellet machine. If the feeding is as well quick, the machine will be overwhelmed. If the feeding is too slow-moving, The inside of the poultry pellet processing machine will certainly be empty, making it more difficult to run. For that reason, the consistent rate of feeding can not only ensure the typical procedure of the pellet machine, however also enhance the functioning performance of the cattle feed manufacturing plant.